The Beneficiation Process of Tin-containing Polymetallic Sulfide Ore
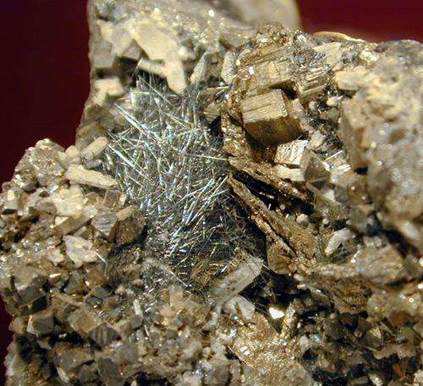
Overview
There are many types of minerals in tin-containing polymetallic sulfide ores. In addition to cassiterite, the main metal minerals include sphalerite, galena, chalcopyrite, pyrite, pyrrhotite, arsenopyrite, etc. Common gangue minerals include quartz, calcite, feldspar, tourmaline, and so on.
The structure and structure of the ore are relatively complex. Cassiterite is densely co-existed with various sulfide minerals, and the proportions of sulfide minerals and cassiterite are close. Due to the above-mentioned characteristics of the ore, it is often difficult to effectively extract cassiterite using only the gravity beneficiation method, and a combination of multiple methods is usually required.
The Beneficiation Process of Tin-containing Polymetallic Sulfide Ore
In practice, the following combined processes are commonly used to select tin-containing polymetallic sulfide ores.
1. Gravity Beneficiation-flotation Process
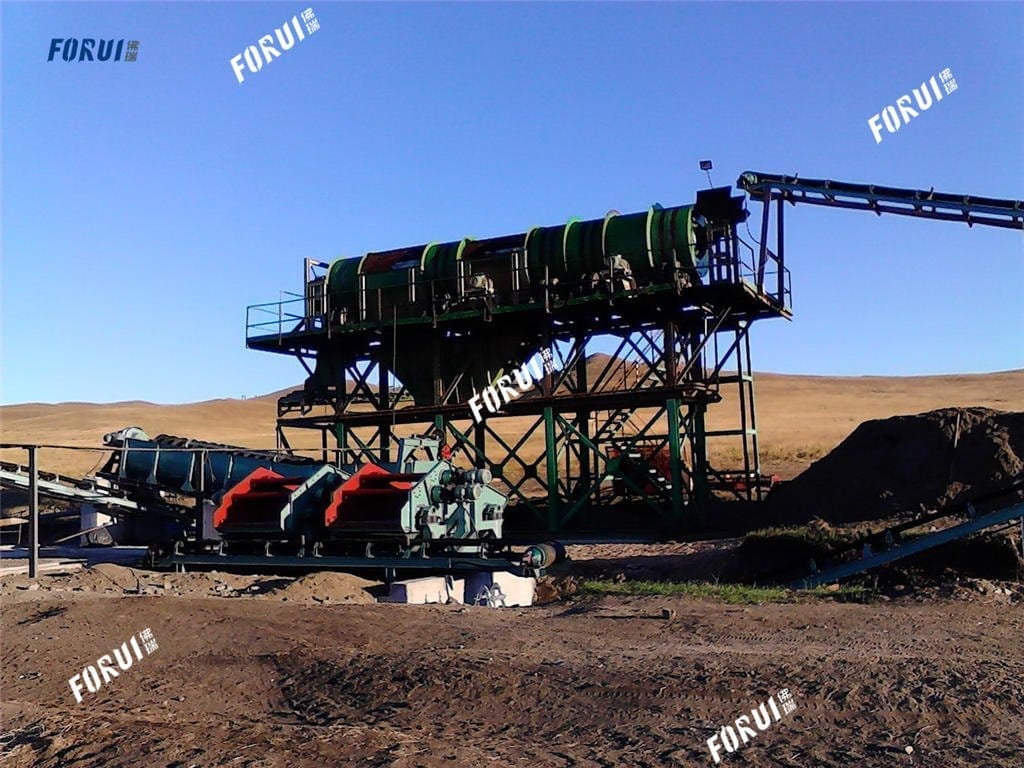
The principle flow is shown in Figure 10-2. That is, after the raw ore is ground, the cassiterite-sulfide mixed coarse concentrate is first selected by gravity beneficiation methods such as a jig or shaker, and the tailings are discarded. Then the coarse concentrate is ground, the concentrate obtained by flotation is sulfide ore, and the tailings from flotation are tin concentrate. This process is suitable for ores with the following characteristics:
- Ore containing less pyrrhotite (generally less than 10%).
- Ore with complex symbiosis relationship between cassiterite and various metal sulfides.
- The inlaid cloth has a finer grain size, mostly in the form of finely crystalline ore.
The Solnech concentrator in the Soviet Union and the Otani tungsten steel and tin concentrator in Japan all use this process.
In some concentrators, the ore is more difficult to be selected, and a combined gravity beneficiation-flotation-roasting process may be adopted. Such as Bolivia’s Corqueli Concentrator, Santa Fe Concentrator and Moroccan Cara Concentrator. Among them, the Kerquili Concentrator classifies the tailings after the zinc-sulfur mixed flotation, and the overflow of the classifier (including hoe <48%) is roasted.
2. Gravity Beneficiation-flotation-gravity Beneficiation Process
Gravity beneficiation of the raw ore obtains a mixed coarse concentrate containing cassiterite-sulfide, and most of the tailings are discarded. The mixed coarse concentrate is then ground and floated to obtain a sulfide concentrate. The flotation tailings are subjected to gravity beneficiation to obtain high-grade tin concentrate.
For example, my country’s Changpo Mine Concentrator currently uses this process to process this tin-containing polymetallic sulfide ore. In addition, such as the Morinos Concentrator and Machakamarca Concentrator in Bolivia, the Krasno Concentrator in the Czech Republic, the Adenburg Concentrator in the Democratic Republic of Germany, the Stalinsk Concentrator in the Soviet Union, and the Givor Concentrator in the United Kingdom Plants, etc. c), all adopt the combined process of multi-stage grinding and multi-stage separation of gravity beneficiation-flotation-gravity beneficiation.
This process is suitable for ore with low pyrrhotite content (generally <10%), complex symbiosis relationship between cassiterite and various metal sulfides, and useful minerals that are mainly fine-grained and unevenly distributed.
3. Flotation-gravity Beneficiation Process
The principle flow is shown in Figure 10-4. This process applies to:
(1) Concentrators focusing on the recovery of tin: when the original ore contains more than 0.5% tin and the content of pyrrhotite is high (generally >10%), the cassiterite and metal sulfide in the ore are fine-grained and dense Symbiosis, more use of this process.
For example, a beneficiation plant of China Yunxi Company, a certain tin mine in Hunan, etc. Foreign countries such as the Cleveland Concentrator in Australia and the Whirljan Concentrator in the UK all use this process for production.
(2) Concentrator with cassiterite as a by-product: When the grade of the original ore is generally between 0.05-0.3%, but the metal sulfide content is high, this process is often used.
Gongyi Forui Machinery Factory is a high-quality enterprise specializing in the production of beneficiation equipment. Over the years, it has produced gravity beneficiation, magnetic separation, flotation, and other beneficiation equipment, and has accumulated a lot of practical experience. Forui Machinery is involved in lead-zinc ore, gold ore, fluorite, barite, pyrite, hematite, limonite, magnetite, manganese ore, antimony ore, tungsten ore, tin ore, celestite, etc. In the field of beneficiation of a variety of minerals, fruitful results have been achieved.
If you need equipment quotation and process flow, please feel free to Contact Us:
- Whatsapp: +8618026978087
- Email: asa.guo@foruimining.com
- Tel: +86-371-64391589
- Facebook: https://www.facebook.com/ForuiMachinery/
- Instagram: https://www.instagram.com/foruimining/
- Twitter: https://twitter.com/ForuiMachinery
- LinkedIn: https://www.linkedin.com/in/asa-guo-benefication-equipment-at-forui/