Discussion on Crushing Theory in Gold Processing Industry
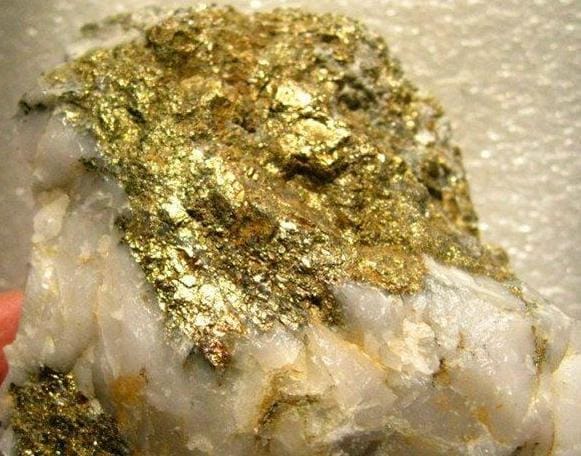
Why is it important to study the crushing theory in gold processing industry for gold ore dressing? Research on the crushing principle in gold processing is very important for the improvement of beneficiation indexes and the control of beneficiation costs.
First, in the beneficiation process of vein gold mines, the crushing process will have a great impact on the beneficiation index. In addition to vein gold mines, the crushing process is one of the work processes that must be completed in the beneficiation of other rock mines.
Second, in the beneficiation plant, most of the electrical energy is used to grind the ore, and the electricity consumption of the ore grinding accounts for more than 60% of the total power consumption of the ore dressing. Therefore, controlling the cost of crushing and grinding is very important to controlling the production cost of the concentrator.
Let’s share the crushing principle of beneficiation.
Catalog of Crushing Theory in Gold Processing
1.Introduction to Crushing Theory in Gold Processing2.The Crushing Purpose of Beneficiation
3.Technical Indicators of Crushing Process
4.Representation of Crushing Ratio
5.Crushing Section and Grinding Section
6.Evaluation Index of Crushing Process
7.Mechanical Strength of Rock Minerals
8.Ore Hardness Grade
9.Crushability and Grindability
10.Force of Crushing Machinery
11.The Microscopic Process of Rock Mineral Fracture
12.The Characteristics of Material Crushing
1.Introduction to Crushing Theory in Gold Processing
The crushing process refers to the use of external force to overcome the cohesive force between the various particles inside the particle, thereby the process of breaking material pieces into small pieces.
According to the action form of the crushing force and the particle size of the product, the crushing process of ore is often subdivided into crushing and grinding:
Crushing: The crushing force is mainly the compressive stress. When the product size is greater than 5mm, it is called Crush.
Grinding: Grinding is mainly achieved by grinding and impact, and when the product size is less than 5mm, it is called Grind.
2.The Crushing Purpose of Beneficiation
The purpose of crushing is to prepare useful minerals and gangue minerals for beneficiation.
In the broken ore, some particles contain only one kind of mineral called monomer dissociated particles. Some particles are connected with other minerals called continuous particles. The separation of the minerals that make up the ore is called monomer dissociation.
Degree of mineral liberation: Refers to the number of useful minerals dissociated into monomers (f) and the percentage of the sum of (f) plus the number of useful minerals co-grown with gangue minerals (∑fi)
Consequences of insufficient dissociation:
- the index of the beneficiation process is unstable.
- the recovery rate is low.
- the grade of the concentrate is low.
- the grade of the tailings is high.
- the yield of the medium block is large.
Consequences of over-crushing:
- high power and material consumption.
- fast machine wear.
- resulting in particles that are difficult to separate.
- resulting in low concentrate grade and recovery rate.
3.Technical Indicators of Crushing Process
The technical indicators of the crushing process mainly include crushing ratio and crushing efficiency. The crushing ratio (i) characterizes the degree of crushing of the material through the crushing process, that is, the ratio of the feed size to the product size. The formula is as follows:
4.Representation of Crushing Ratio
(1) Maximum crushing ratio (Ultimate crushing ratio)-ratio of maximum block size
(2) Nominal crushing ratio-ratio of a crusher’s feed port size to the discharge port size
- 0.85B — the effective width of the mine mouth
- S — the width of the mine outlet
(3) Average crushing ratio (true crushing ratio)-ratio of average particle size
The maximum crushing ratio and common crushing ratio of various crushers
The table is as follows
Name | Max Crushing Ratio | Rated Crushing Ratio |
---|---|---|
Coarse Jaw Crusher | 8~10 | 3~5 |
Medium Cone Crusher | 15 | 4~7 |
Fine Cone Crusher | 15 | 4~7 |
Sectional Crushing Ratio and Total Crushing Ratio
Sectional Crushing Ratio
- From the largest block to the particles suitable for the mineral processing requirements, the size crushing ratio can reach tens of thousands of times. One crushing cannot complete the task, and the corresponding operation must be completed through the cooperation of crushing and grinding.
- The crushed ore can be divided into 1~3 sections according to the particle size, primary crushing i1, medium crushing i2, and fine crushing i3.
- Grinding can be 1~2 stages according to the requirements of mineral processing particle size, primary grinding i4, fine grinding i5.
Total crushing ratio: the product of the crushing ratio of each section
5.Crushing Section and Grinding Section
In the beneficiation plant, crushing and grinding are divided into two major stages according to the structural characteristics of the equipment used and the range of particle sizes suitable for processing, and each major stage includes several smaller stages.
Basis for stage division: Particle size of useful minerals embedded in ROM(run of mine), the particle size requirements of the product, and the special requirements of the entire process on the ore. To sum it up, the different stages of crushing and grinding are the whole process of using several crushing and grinding equipments for processing different particle sizes to gradually crush the raw ore to the specified selected particle size.
Crushing is the forerunner of ore grinding, and grinding is the continuation of crushing.
– | Stage | Feed Diameter (mm) | Product Diameter (mm) |
---|---|---|---|
Crushing | Coarse Crushing Secondary Crushing Fine Crushing | 1500~300 350~100 100~40 | 350(450~125) 100~40 30~10 |
Grinding | Primary Crushing Fine Crushing | 30~10 1.0~0.3 | 6~2 < 0.1 |
6.Evaluation Index of Crushing Process
Crushing Processing Capacity
It is expressed in terms of the amount of ore processed per unit time, t/h, to evaluate the crushing process quantitatively.
Crushing Efficiency
The crushing efficiency is usually defined as the number of tons of crushed products obtained per 1 kw·h of energy consumed.
Expressed by the unit energy consumption of crushed ore, t / kw•h, to evaluate the crushing process from the energy consumption.
7.Mechanical Strength of Rock Minerals
The mechanical strength of rock minerals refers to the resistance to external forces when the ore is crushed. The compressive strength, tensile strength, flexural strength, shear strength, etc. of the ore measured under static load are commonly used to express the crushing resistance of the rock minerals-mechanical strength.
The smaller the particle size, the greater the compressive strength of the load, and the harder the ore is to crush.
In production practice, materials are often divided into three levels of hard, medium hard, and soft or very hard, hard, medium hard, soft and very soft according to their mechanical strength.
The Protodyakonov Coefficient f (Russian Protodyakonov) is usually used to express the firmness of the ore, or firmness coefficient. The figure is 1% of the uniaxial compressive strength limit of the rock:
f =0.3~20, the larger f is, the harder the ore, and the harder it is to be grinded
8.Ore Hardness Grade
Ore Hardness Grade | δ Pressure (kg/cm2) | Platts Hardness Coefficient | Crushability Coefficient | Grindability Coefficient | Examples |
---|---|---|---|---|---|
Very Soft | <200 | <2 | 1.3-1.4 | 2.00 | Gypsum Stone Slate |
Soft | 200-800 | 2-8 | 1.15-1.25 | 1.50 | Limestone |
Medium Hard | 800-1600 | 8-16 | 1.0 | 1.0 | Quartz Sulfide Ore |
Hard | 1600-2000 | 16-20 | 0.8-0.9 | 0.75 | Silicified Shale Iron Ore |
Very Hard | >2000 | >20 | 0.65-0.75 | 0.5 | Hard Granite |
9.Crushability and Grindability
Crushability and grindability reflect the difficulty of ore being crushed, and it depends on the mechanical strength of the ore. In the same crushing machine, under the same conditions, compared to processing hard ore and soft ore, the productivity of the former case is lower and the power consumption index is larger.
The crushability coefficient and grindability coefficient of the ore proposed in combination with the crushing and grinding technology not only reflect the firmness of the ore, but also can be used to quantitatively measure the process indicators of the crushing machinery.
Crushability Coefficient Formula:
Grindability Coefficient Formula:
- Medium-hard minerals generally refer to ores such as quartz, and their crushability coefficient and grindability coefficient are both equal to 1.
- Kcrushing, Kgrinding>1, the ore is soft, easy to crush and grind.
- Kcrushing, Kgrinding<1, the ore is hard, difficult to crush and grind.
10.Force of Crushing Machinery
There are five main types about force of crushing machinery:
- a. Squashing (reflecting compressive strength)
- b. Splitting (reflects tensile strength)
- c. Snapping (reflects bending strength)
- d. Impact (reflects impact resistance)
- e. Grinding (reflecting shear strength)
- A crushing equipment may have several force methods at the same time, but mainly one or two types of force.
- The choice of force application method mainly depends on the hardness and brittleness of the ore.
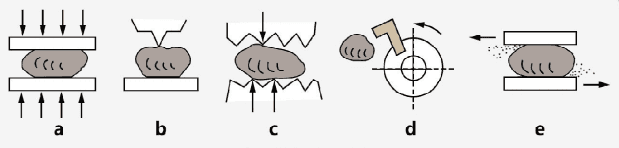
Squashing: mostly used for primary crushing of brittle and hard materials. Splitting: It is most beneficial to the crushing of materials. Impact: mainly used for crushing brittle materials. Grinding: It is mostly used for fine grinding of small pieces of material.
Schematic diagram of crushers:
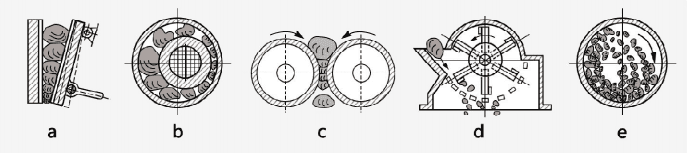
11.The Microscopic Process of Rock Mineral Fracture
1.Apply force
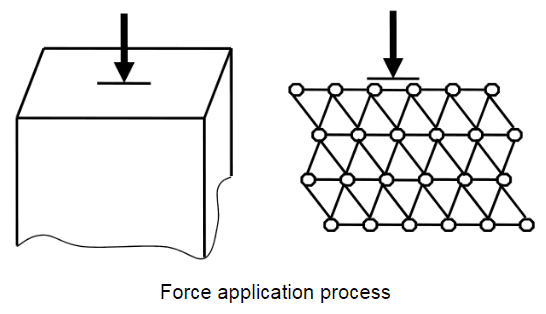
2.Deformation
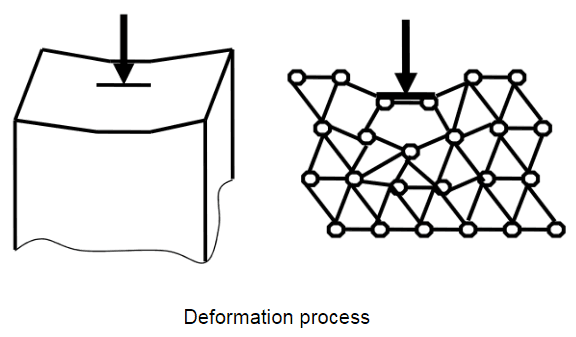
3.Crack formation and propagation
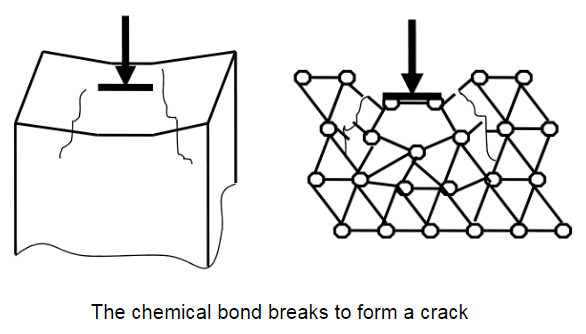
4.The formation of new surface (fracture)
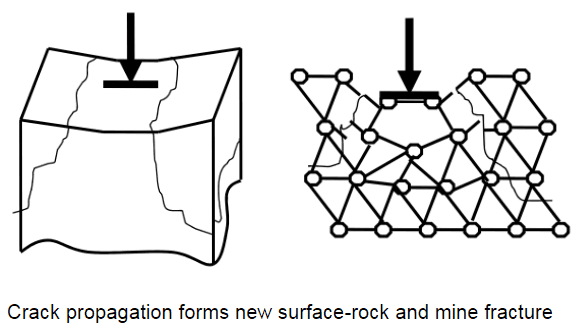
5.Loss of external force and recovery of deformed parts
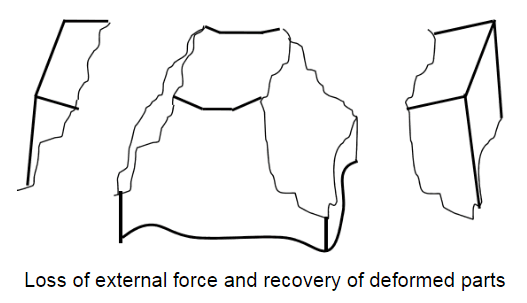
12.The Characteristics of Material Crushing
In the crushing process, the crushing machine does work on the material to deform it. When the deformation exceeds the limit, it will be broken.
After the breakage occurs, a small part of the work done by the external force is transformed into the surface energy of the new surface, and most of the rest is lost in the form of heat. Only about 6% of the energy input by rock minerals grinding is converted into useful work required.
From a macro perspective, the crushing process of materials is a process of particle size reduction (that is, the process of gradual monomer dissociation of minerals), but its mechanical essence is an energy conversion process.
The power consumption theory of material crushing is the theory about the function conversion law in the material crushing process. That is, the research on the relationship between the energy input to the crushing process and the particle size of the product under a certain feed size condition.
In the beneficiation plant, most of the electric energy is used to crush and grind the ore, accounting for more than 60% of the total power consumption of the beneficiation. Therefore, controlling the cost of grinding is very important to controlling the production cost of the concentrator.
Summary
First, the crushing process will have a great impact on the beneficiation index of other rock mines. Second, in the beneficiation plant, most of the electrical energy is used to grind the ore, and the electricity consumption of the ore grinding accounts for more than 60% of the total power consumption of the ore dressing.
Therefore, controlling the efficiency of crushing and grinding is very important to improve the beneficiation index and control the production cost of the beneficiation plant.
Thank you for reading. What are your thoughts on the crushing theory in gold processing? Welcome to leave a message, or contact me directly:
- Email: asa.guo1989@gmail.com
- Whatsapp & phone: +8618026978087
Gongyi Forui Machinery Factory, founded in 1986. We are one of the leading suppliers of gold wash plant equipments in Asia. Don’t hesitate to Contact Us, if you have any question of beneficiation. And welcome to visit our company. Gongyi Forui Machinery Factory dedicated to serve you!
Responses